Maximizing Efficiency and Profitability: Understanding Pigging System ROI
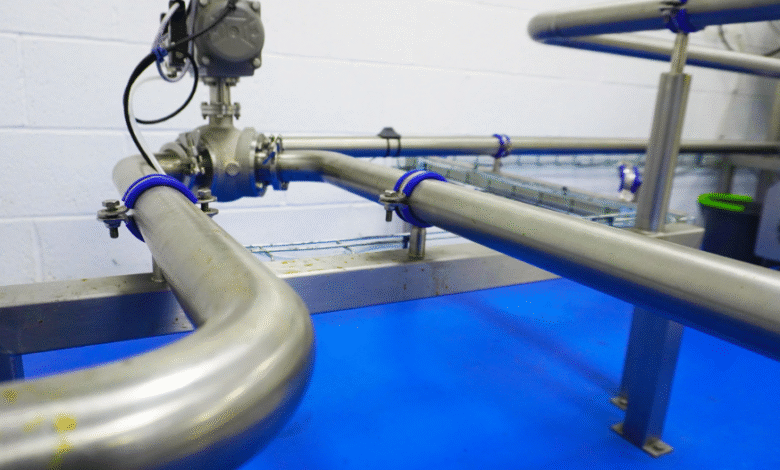
In industries where pipelines are the backbone of production and transportation—be it in oil, gas, chemicals, pharmaceuticals, or food and beverage—maintaining product integrity and operational efficiency is paramount. Among the tools that have proven to deliver both is the pigging system. Beyond its technical benefits, one of the strongest arguments for its implementation lies in the pigging system ROI, or return on investment.
But how do we quantify this return, and what are the financial and operational metrics that justify the upfront cost of pigging technology? This article explores the components of pigging system ROI and why it has become an indispensable strategy for companies aiming for sustainability, productivity, and profitability.
What Is a Pigging System?
A pigging system is a technology used to recover product, clean pipelines, and prevent cross-contamination without dismantling the pipeline or interrupting the production flow. It uses a device known as a “pig” that travels through the pipeline, pushed by pressure from the product itself or a propellant like nitrogen or air.
Modern pigging systems are far more than simple pipeline cleaners. They are smart, automated systems integrated into production processes to boost efficiency and reduce waste—key drivers of ROI.
See also: Editing for Narrative Storytelling: Tools and Techniques
Understanding Pigging System ROI
So, what exactly is pigging system ROI It refers to the measurable return gained by an organization from its investment in a pigging system. The ROI is calculated by evaluating:
- Cost savings (from reduced waste, cleaning time, labor, and utility usage)
- Recovered product value
- Decreased downtime
- Improved compliance and product quality
- Reduced environmental impact and chemical disposal costs
For many businesses, ROI is not a long-term expectation—it is often achieved in under two years and in some cases, within just a few months.
Factors That Affect Pigging System ROI
1. Product Value
The higher the value of the product being transported through the pipeline, the greater the potential for recovered product revenue.
2. Pipeline Design
The length, diameter, and frequency of use all impact how much product can be recovered and how much cleaning is needed.
3. Production Volume
Facilities operating multiple batches per day with frequent product changeovers benefit significantly, leading to faster ROI.
4. Labor and Utility Costs
The savings on labor hours, water usage, chemical use, and disposal charges add significantly to the return.
5. Downtime Reduction
A pigging system that allows cleaning or product transitions without stopping operations can save thousands in lost production time.
Breakdown of ROI Components
Let’s take a closer look at the individual contributors to pigging system ROI.
✅ Product Recovery
One of the biggest sources of ROI is product recovery. Residual product left in the pipeline after a batch transfer can represent significant value.
Example:
- 15 meters of 2-inch pipeline may hold 3 liters of product.
- If a facility runs 10 batches daily, that’s 30 liters left behind each day.
- For a product worth $5 per liter, that’s $150 per day—$54,750 annually.
Pigging can recover more than 95% of this residual material, directly boosting revenue.
✅ Reduced Cleaning Time
Traditional pipeline cleaning methods require disassembly or extensive flushing with water and chemicals. Pigging drastically reduces this time.
Impact:
- Cleaning time can drop from 1 hour to 10 minutes.
- If labor costs $30/hour and cleaning is done twice daily, that’s $18,000 saved annually per line.
✅ Lower Utility Consumption
Pigging uses significantly less water, energy, and chemicals. This leads to:
- Reduced water and chemical bills
- Lower environmental fees and fines
- Less wastewater and disposal cost
✅ Improved Product Quality
Avoiding cross-contamination during product changeovers ensures better product integrity. That translates to:
- Fewer recalls
- Higher customer satisfaction
- Improved brand reputation (hard to quantify, but critical)
✅ Equipment Longevity
Because pigging removes abrasive particles and contaminants, it extends the lifespan of pumps, valves, and pipes. This reduces repair costs and downtime.
Industry Examples: Pigging System ROI in Action
🧃 Beverage Manufacturing
A juice processing plant uses a pigging system between flavor batches. Previously, each batch transition lost around 20 liters of juice.
ROI Breakdown:
- Recovered Product: 20L × $4 = $80/batch
- 500 batches/year = $40,000 saved
- Cleaning water and labor savings = $12,000/year
- Total annual ROI: $52,000
- System cost: $35,000 → ROI achieved in less than 9 months
🧪 Chemical Blending Facility
Frequent batch changeovers caused solvent usage of 1,000 liters/month and $6,000/year in waste disposal fees.
Post-Pigging:
- Solvent usage dropped by 75%
- Waste disposal reduced to near zero
- Downtime cut by 40 hours/month
- ROI achieved within 13 months
Environmental Benefits as ROI Contributors
While environmental impact may seem hard to monetize, regulations are becoming stricter globally. Pigging helps facilities stay compliant with:
- Wastewater discharge permits
- Chemical storage and usage limits
- Carbon footprint reporting
Avoiding fines, gaining certifications (ISO, GMP), or simply improving ESG (Environmental, Social, and Governance) scores can all enhance a company’s financial performance.
Implementing a Pigging System for Best ROI
To maximize pigging system ROI, companies should follow key best practices:
✔️ Conduct a Product Loss Audit
Understand how much product is currently being lost. This sets a baseline for recovery estimates.
✔️ Customize the System
Pigging systems must match the product’s viscosity, pressure requirements, and pipeline configuration. Off-the-shelf solutions rarely provide optimal results.
✔️ Automate Where Possible
Automated pigging reduces manual labor, increases precision, and enhances consistency.
✔️ Train Staff
ROI depends on correct system use. Investing in proper training ensures safe and efficient pigging operations.
✔️ Monitor KPIs
Track metrics like product recovery rates, cleaning time saved, and downtime reduction to evaluate ROI over time.
Future Trends: Increasing ROI Through Innovation
Technological advancements are pushing pigging system ROI even higher. Innovations include:
- Smart pigs with real-time data feedback
- IoT-based pig tracking and system diagnostics
- Eco-friendly pigs made from biodegradable materials
- Predictive maintenance tools to avoid unexpected system failures
These additions not only enhance pipeline performance but also make pigging smarter, greener, and more profitable.
Conclusion
The pigging system ROI is not just about recouping an equipment investment—it’s about transforming operational efficiency, minimizing waste, and maximizing profits. From product recovery to reduced labor costs and better quality control, the financial and strategic benefits make pigging systems a smart decision for any pipeline-based process.
Companies that invest in pigging today are not only improving their bottom line but also paving the way for a more sustainable and efficient future. In industries where margins are tight and quality is king, pigging doesn’t just pay for itself—it pays dividends.